ConeAct: A Multistable Actuator for Dynamic Materials
Yuyu Lin, Jesse T. Gonzalez, Zhitong Cui, Yash Rajeev Banka, Alexandra Ion
Publication: In CHI Conference on Human Factors in Computing Systems (CHI '24). DOI: https://doi.org/10.1145/3613904.3642949
Abstract. Complex actuators in a small form factor are essential for dynamic interfaces. In this paper, we propose ConeAct, a cone-shaped actuator
that can extend, contract, and bend in multiple directions to support rich expression in dynamic materials. A key benefit of our actuator is that it is self-contained and portable as the whole system. We designed our actuator’s structure to be multistable to hold its shape passively, while we control its transition between states using active materials, i.e., shape memory alloys. We present the design space by showcasing our actuator module as part of selfrolling robots, reconfigurable deployable structures, volumetric shape-changing objects and tactile displays. To assist users in designing such structures, we present an interactive editor including simulation to design such interactive capabilities.
Keyword: Dynamic materials, Fabrication, Programmable Matter
Applications: Programmable Matter
Working principle: multistable structures inspired by bendy-straw
p
p
Small Title
pl
Multistable conical structure
Our ConeAct requires no external force to maintain its shape in the (a) extended, (c) contracted or (e) bent state.
Transitioning between states: SMAs
We integrate four such SMAs into our cone structures to push and pull them between their multiple stable states. One coil-shaped wire in the center serves as a "contractor", compressing the module when active; and three straight wires along the perimeter serve as "extenders", allowing the module to stretch and bend.
Fabrication
A ConeAct module
Materials:
SMA wire: 375 µm diameter, 70ºC
SMA coils: 381 µm diameter, 10 coils, 90ºC
3D Models: TPU cone and ABS stiffeners
First, the SMA "extender" wires are cut to 30 mm lengths, and soldered to the bottom PCB, along with the "contractor" coil (a). The 3D-printed TPU cone, along with ABS stiffeners, is fixed to the bottom PCB — a small wire is hooked through both the PCB and the ABS stiffener (b-c). The cone is then pushed to a retracted, stable state, allowing access to the SMA contractor coil (d), which are soldered to the upper PCB (e).
As a final step, the ABS lid of the cone is glued to the upper PCB (f). After the fabrication process, the SMA extenders are approximately 25 mm long (from the lower solder joint to the upper solder joint).
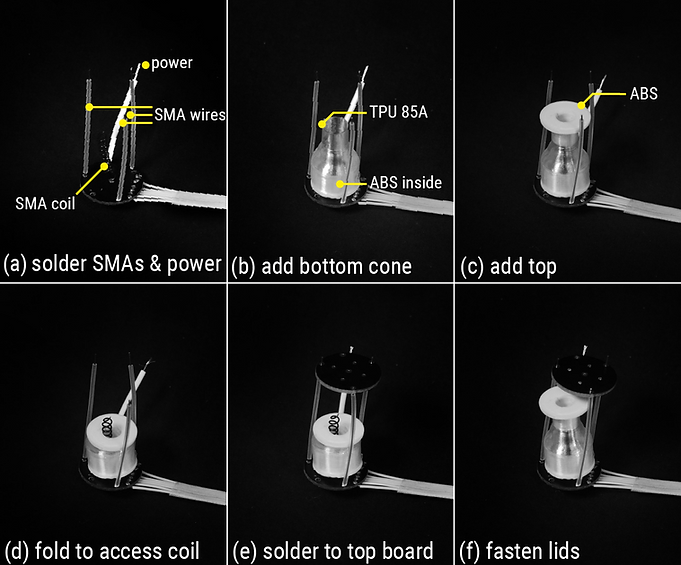
Electronic Control
PCB designs: controller PCB, sensing PCB, and their programmer; module connectors
programming code (Arduino Nano): instructions and code
control code (Arduino): code
Two custom circuit boards (16 mm in diameter) sit on the top and bottom of our ConeAct module. The bottom circuit board houses two dual MOSFETs (Texas Instruments CSD87502Q2), each capable of switching up to 5A (though in practice, we limit the current draw to 2.5A). Each MOSFET drain is connected to one end of an SMA wire. The top circuit board acts as a shared power plane, providing a path for the actuator current (a 28 AWG wire connects the two boards). We drive the gates of the MOSFETs with a small onboard microcontroller (ATTiny1616), operating
at 3.3 V. For each actuator, a watchdog timer (which can be set and reset by an external command) will shut off the appropriate MOSFET, to avoid overheating the SMA wire.
The onboard microcontroller responds to commands issued from a separate "director" device (an Arduino Nano) over an I2C bus. (These commands are simple instructions that activate an actuator and set its corresponding timer.) From this director device, we can address and control numerous ConeAct modules (a necessary requirement, since we use multiple modules to compose larger structures).
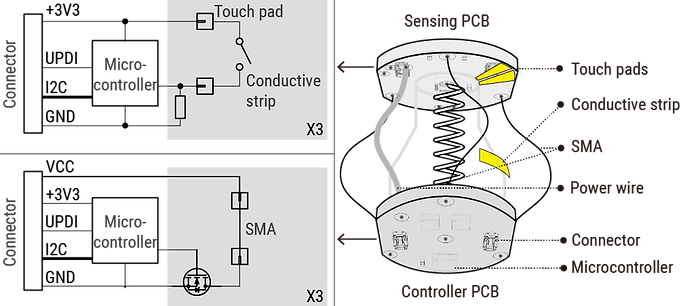
Controlling Multiple Actuators
Our modules can be chained together using flexible connectors that mate with the lower PCB. Once connected, these modules share a power
source and I2C bus, allowing for communication with a single director device.
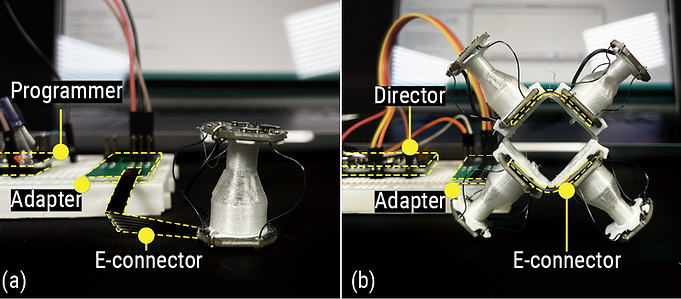
Full video